我公司是專業的換熱器管板加工廠商。在換熱器管板制造過程中,鉆孔是一道工作量大且有一定難度的工序。一塊管板上要加工上千個孔。且孔的尺寸精度、位置度、垂直度和孔徑表面粗糙度都有一定的要求。對于長徑比小于4的孔,在搖臂鉆床上用普通麻花鉆一次鉆削完成,可達到精度要求。隨著管板厚度尺寸的增大,難度就隨之增大。現將換熱器管板深孔的鉆削加工介紹如下:
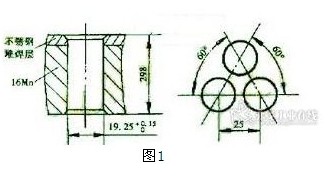
1工件的鉆削要求
需加工的管板厚度298mm(見圖1).材料為16Mn+堆焊不銹鋼。過渡層用3O9L焊材,堆焊厚度3mm;面層用347L焊材.堆焊厚度3mm。管板鉆孔后,≥96%的孔橋寬度必須≥3.4mm,≤4%(且不超過5個孔)的最小孔橋寬度≥2.75mm。
2鉆削加工
2.1工件裝夾
在Z30100搖臂鉆床工作臺上放4個等高墊鐵,使工件下端面離開工作臺有一定間隔.工件裝夾盡量靠近機床立柱,然后在鉆床主軸上裝百分表,沿搖臂方向和垂直于搖臂的方向檢查工作平面的實際高度差.用加薄墊的方法將工件外緣處的差值調整到0.03mm以內,壓緊后再檢查一次。
2.2鉆削加工
為保證孔橋位置的精度,采用鉆模定位,先將鉆模板上的定位刻線對準工件中心線后把鉆模板連同工件壓緊。
鉆孔采用三次分段鉆削然后鉸削的方法,保證孔徑的垂直度和尺寸精度。鉆孔時先用短的鉆頭將所有的孔鉆出定位孔,然后取掉鉆模板,第一次用較短的鉆頭鉆深約100~120mm,然后換長刃鉆頭鉆深約190~210mm,最后用拋物線槽形的鉆頭鉆通。
鉆削用量:n=315r/min,f=0.32~0.4mmm/r;
鉸削用量:n=450r/min,f=0.5mm/r。
2.3鉆頭刃磨
鉆削深孔時排屑是關鍵,容器鋼和不銹鋼的韌性都較大.切屑易變形.若堵在容屑槽內,易劃傷孔壁,影響表面粗糙度。為了使麻花鉆頭也能順利排屑,必須對鉆尖外形進行修磨。
鋒角比標準麻花鉆大,約在130°~140°之間。鋒角增大,刃部的切削扭矩減小,切屑變厚、寬度減窄.切削變形減小而使切屑平直。
橫刃將橫刃修短,可使這部分刃口的前角也比原先的增大,可改善鉆心部分的切削情況,減少鉆削時的擠壓現象,降低鉆孔軸向力,可適當增大進給量并進步鉆頭耐用度。修磨橫刃是公道使用麻花鉆頭,進步鉆削性能的一個重要手段。
后角鉆頭的切削刃是繞主軸旋轉的,切削刃上每個點的后角是不相等的,鉆頭在旋轉的同時,還有軸向進給,這個活動的合成就使鉆頭的實際工作后角比刃磨后角要小,而后角的減少在進給量不變的條件下,隨鉆削刃半徑的減小而增大,進給量越大.減少值越大。因此,增大鉆芯部分的后角是非常必要的,鉆刃上磨有分屑槽后,鉆芯部分的后角就可以單獨刃磨了。
a) 普通麻花鉆頭b)拋物線槽形鉆頭
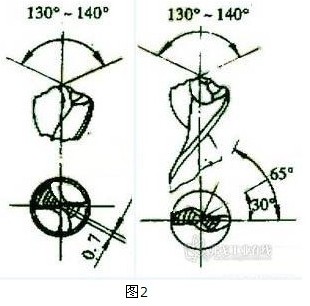
分屑槽采用雙刃分屑槽,在進給量不變的情況下,可以減小切屑寬度和加大切屑厚度。根據切削原理知道:切屑寬度對切削力的影響比切屑厚度大。因此.在相同的切削面積時,窄而厚的切屑比薄而寬的切屑省力。分屑后切屑成直條,排屑時速度快,還可以把部分細碎的帶狀切屑帶出,并使切屑之間、切屑與孔壁之間的相互摩擦、擠壓現象減少。直條切屑所占的空間面積小.有利于冷卻液進進。最后用拋物線槽形鉆頭將孔鉆通(見圖2),它與麻花鉆相比有很多優點。首先是鉆芯增厚,進步了鉆頭的剛性;其次螺旋角增大,容屑槽加寬.使切屑區的容屑空間增大,冷卻條件得到改善。刃磨時,鉆尖采用十字刃磨法.縮短橫刃,減少軸向力;鉆尖部分采用群鉆形式,增大鋒角。雙刃分屑,使較窄的切屑沿鉆頭容屑槽根部直線排出。
冷卻題目搖臂鉆床的冷卻是用泵將冷卻液抽出直接澆注到孔口,自然流進孔內進行冷卻的。鉆孔開始時,可以充分冷卻。鉆到一定深度后.由于切屑排出方向與冷卻液流向相反,冷卻液流到切削區的量逐漸減少,孔越深這種現象越明顯.為了保證鉆頭耐用度。在鉆削過程中,根據不同的工件材質選擇切削用量,摸索出每次鉆深尺寸,然后提鉆,可解決排屑與冷卻的題目。
3結論
采用三次鉆孔后鉸孔的工藝所鉆的管板孔,孔徑尺寸和孔橋寬度完全符合圖紙要求。
|